Before the introduction of the Eurocodes, British Standards did not cover the geotechnical design of steel piles in any detail, although there is general guidance given in BS 8002, BS 6349, and BS 8004.
Reference has also been made to the offshore industry’s recommended practice for steel tubular piles, American Petroleum Institute Code RP 2A and most recently in ISO Code of Practice 19902-2. This has been verified as applicable to steel H-piles by Biddle and Wyld and Jardine et al. Other technical references are also used,such as CIRIA Report 103 The design of laterally loaded piles, CIRIA Report 104 Design of embedded retaining walls in stiff clay, Offshore Technology Conference (OTC) papers and other research papers, and selected textbooks.
With the introduction of BS EN 1997-1:2004, and the UK National Annex, a more rigorous treatment using Limit State Design principles was made possible for foundations and is compatible with structural Eurocodes.
For steel piling, structural design is performed in accordance with BS EN 1993-5 ‘Steel Piling’.
Steel Bearing Piles
Steel piles are relatively light and easy to handle, and can be driven in most types of ground, including many types of rock: H-piles are particularly suitable for this. H-piles are also useful as tension piles because of the large penetrations which can be achieved. Circular and box piles are more suitable where large axial and bending effects are to be resisted (in corrosive conditions they are less vulnerable because they have less exposed surface). The advantages of each type may be employed in a composite pile comprising a bottom H-section, driven to achieve uplift resistance and welded to the inside of a tubular upper section which is used to resist vertical and horizontal actions.
The fracture toughness of welds should conform to BS EN 1993-5. For special steels, the fracture toughness should conform to BS EN 1993-1-10.
Steel piles have good energy-absorption properties and may therefore be used, when installed vertically, to resist horizontally applied actions. If a concrete encasement is added for corrosion protection, the necessary limitations on maximum strain might require the permissible energy absorption to be reduced.
Steel piles can be manufactured in a series of cans (i.e. lengths of steel plate, bent to form a tubular section and welded down the seam), or from spirally welded strips. The manufacture of such piles should be in accordance with BS EN 10210 for longitudinally welded piles and BS EN 10219 for spirally welded piles.
Steel piles may be readily extended by butt-welding an extension piece, and they are therefore useful at sites where the pile lengths cannot be accurately predicted.
Hollow steel piles might be required to be filled with concrete at the toe, when end-bearing capacity is critical, or at the head, when a full bending moment connection to the deck is required.
For structures subject to dynamic actions, suitable impact values for the steel should be specified to prevent brittle fracture.
External corrosion may be minimized by means of protective coatings or cathodic protection or may be allowed for in design Further guidance on steel bearing piles is given in Steel bearing piles guide P156 published by the SCI.
Read more about Durability
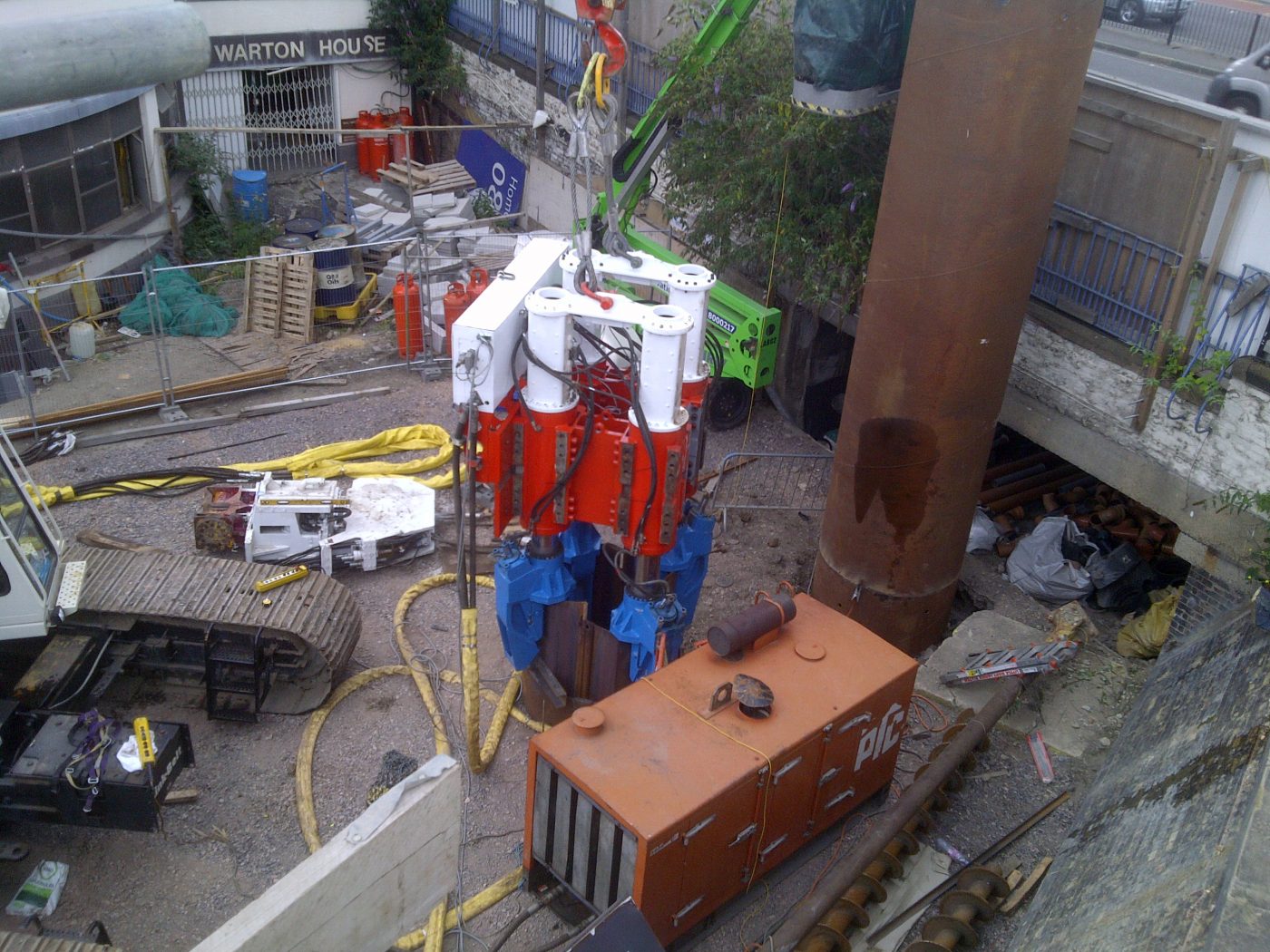
Case Studies
A selection of our work
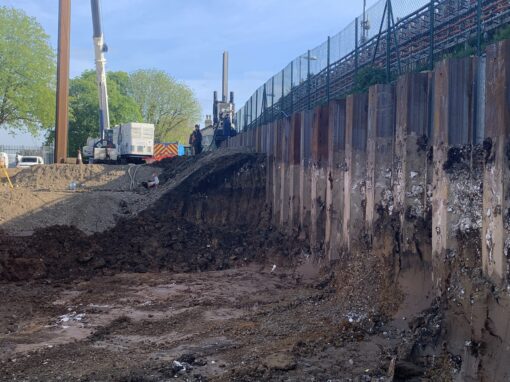
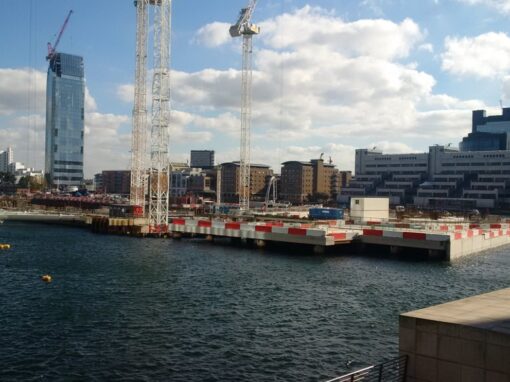
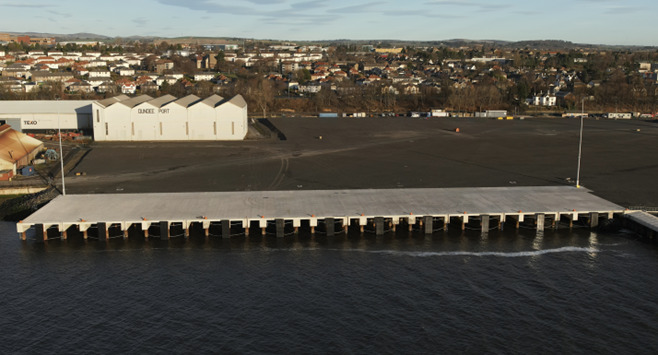
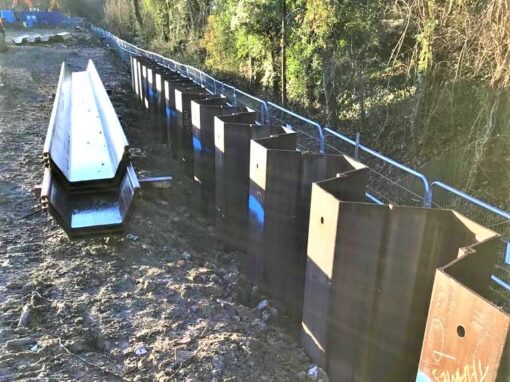

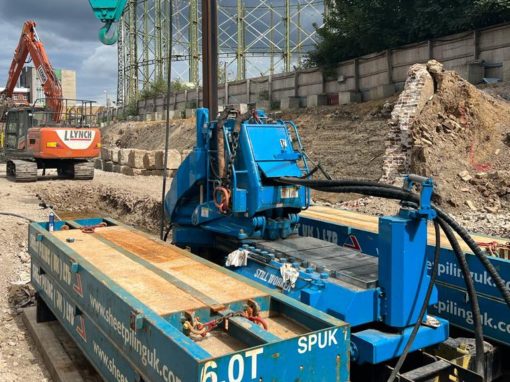

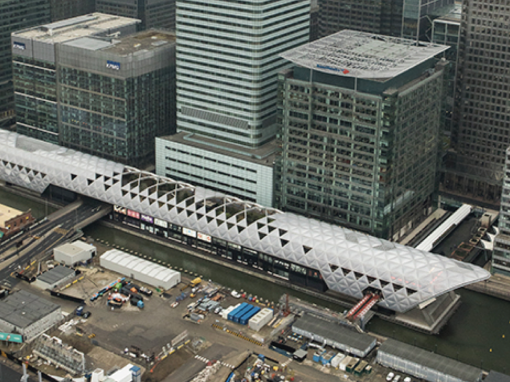
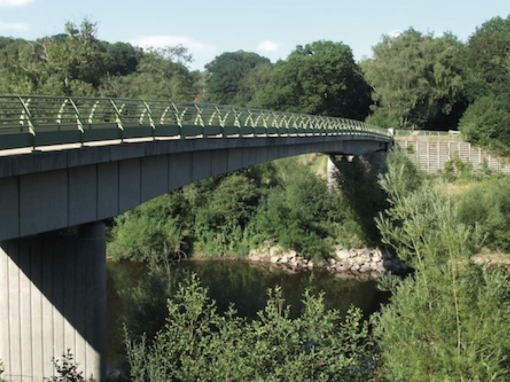
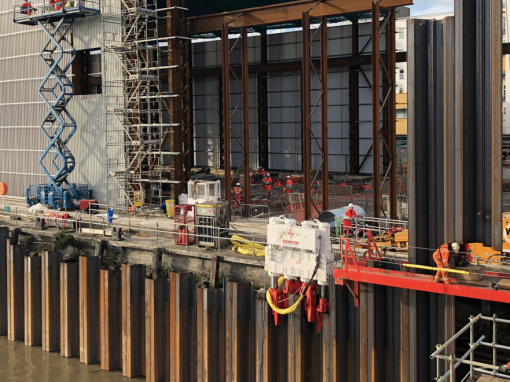
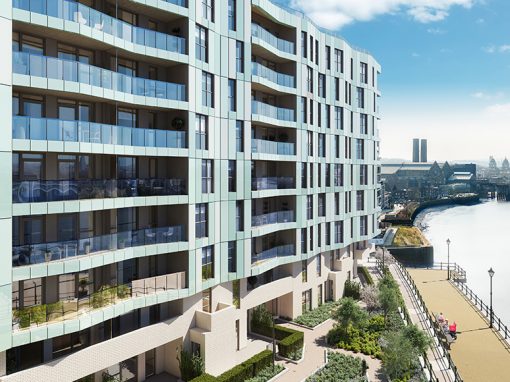
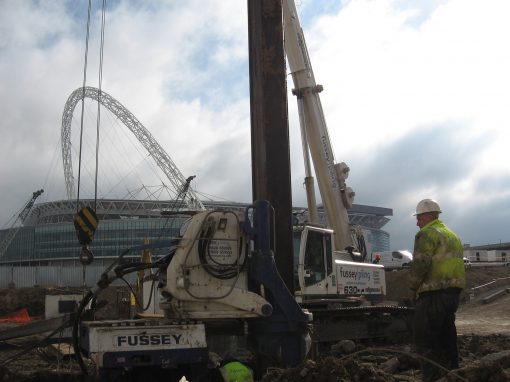
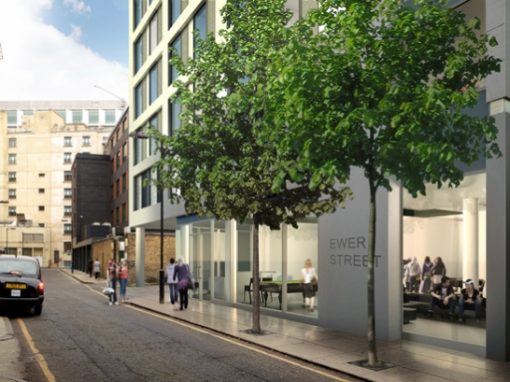
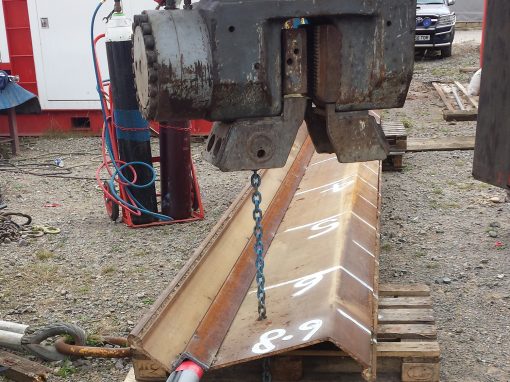
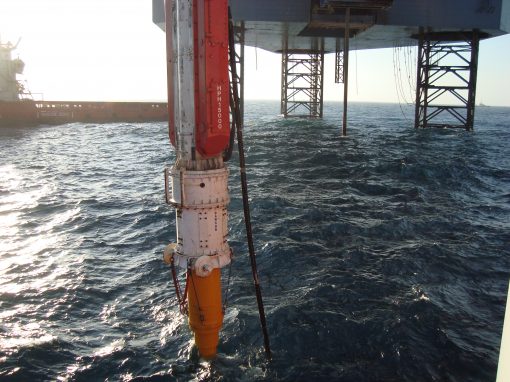
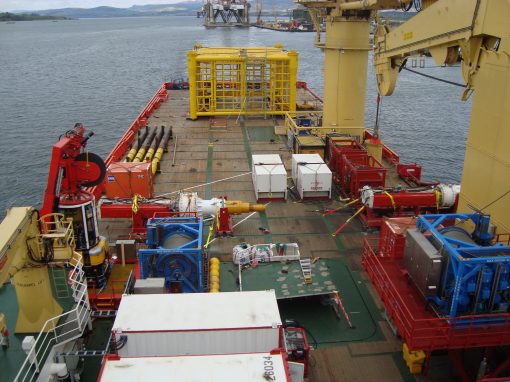
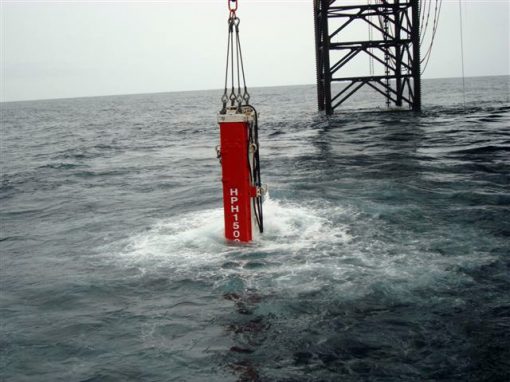
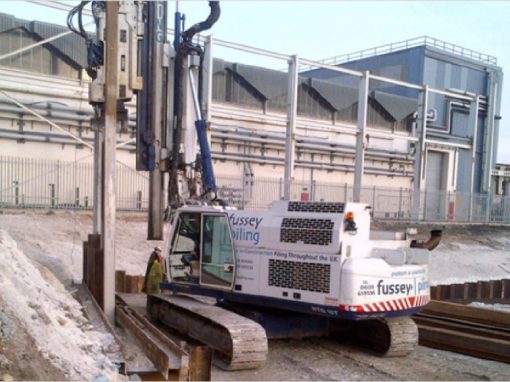
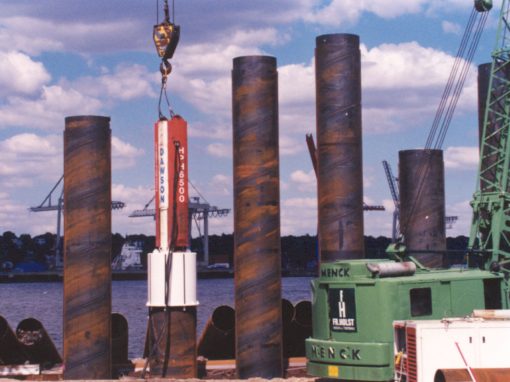
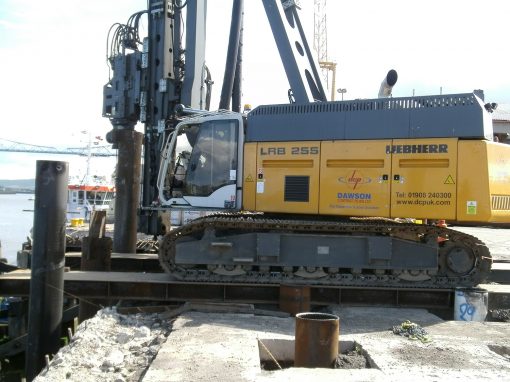
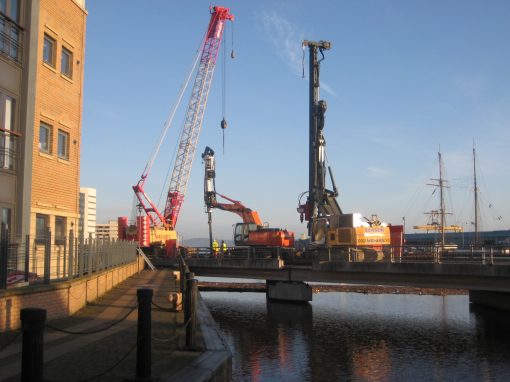
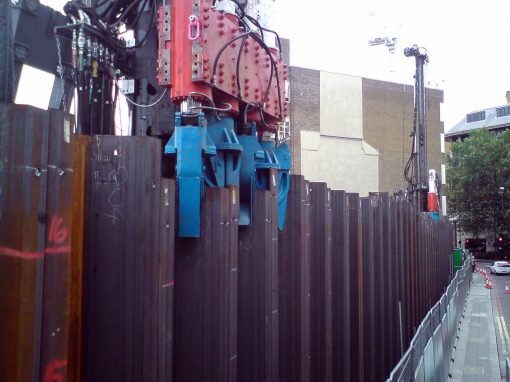
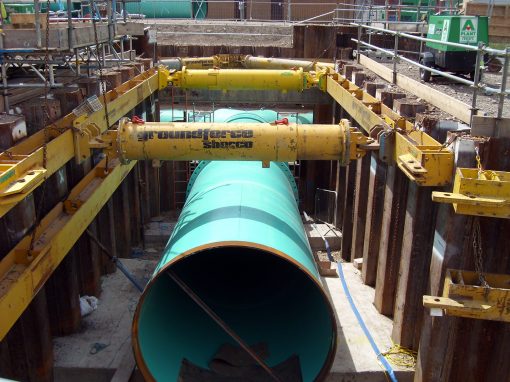
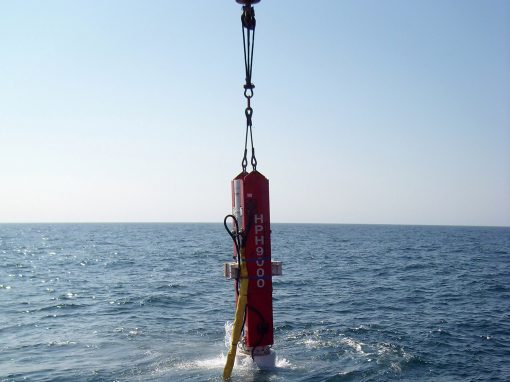
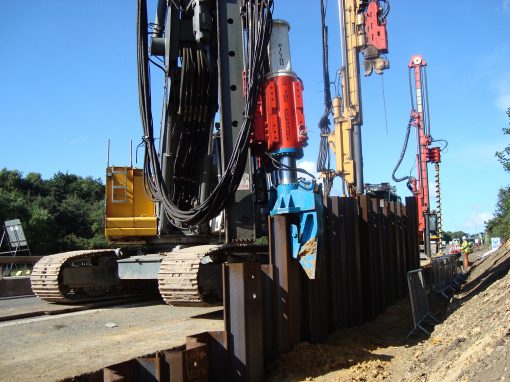
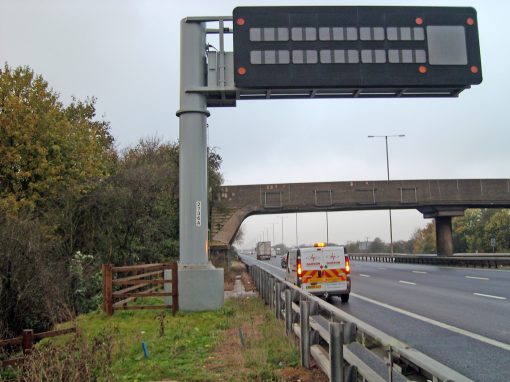
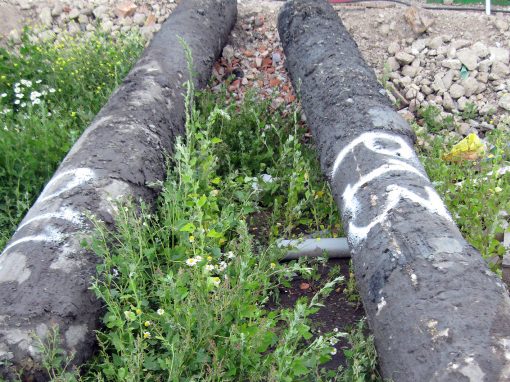
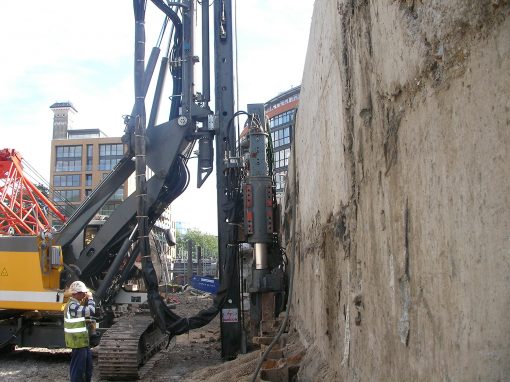
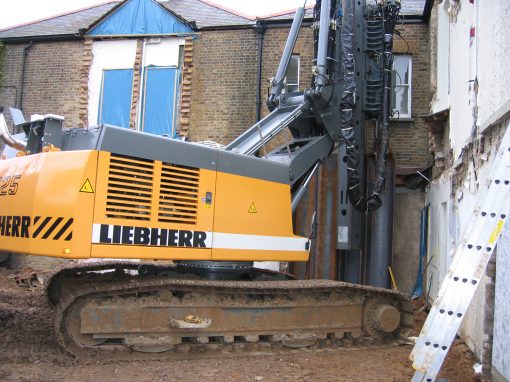
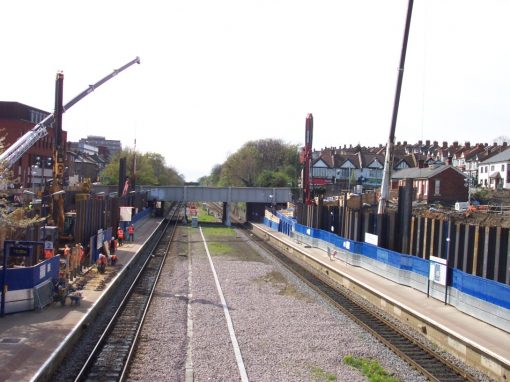
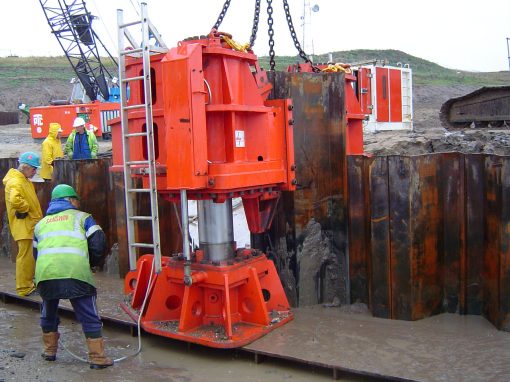
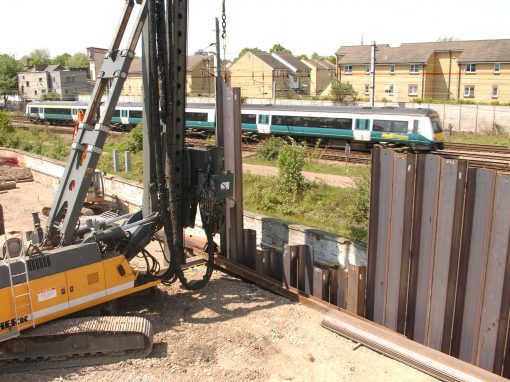
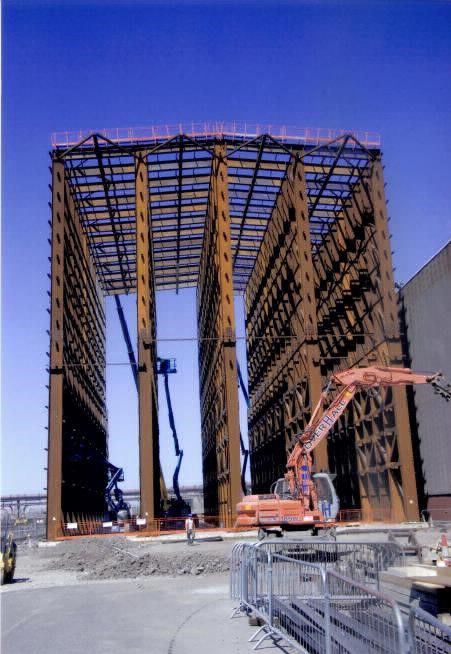
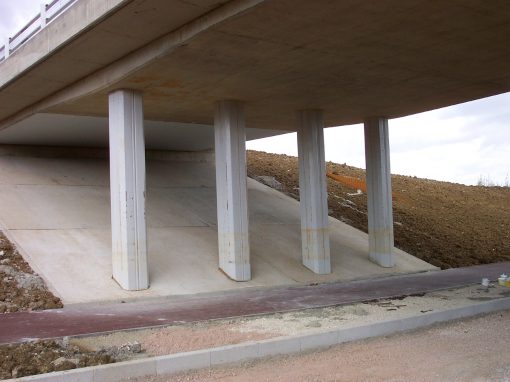
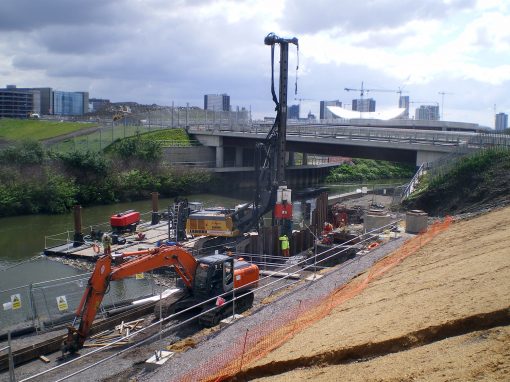

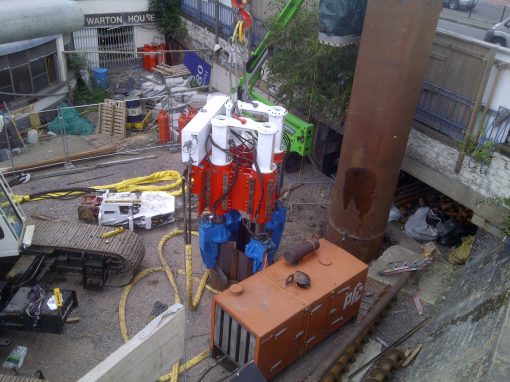
Steel Piling Group, C/O SCI, Silwood Park, Unit D, Buckhurst Road, Ascot ,Berkshire. SL5 7QN
E: info@steelpilinggroup.org
© Copyright 2018 Steel Piling Group
Terms & Conditions | Privacy Policy