Hot rolled steel sheet piling has been manufactured and used for over 100 years. It has continually developed and evolved to make it more useful, more efficient and more sustainable. As a product it has been subject to a metamorphosis in terms of shape, manufacturing, substance, installation plant and capability.
Developments in shape
Over the years the shape of sheet piles has developed. Initially the common sections were narrow U shaped piles because these were easy to drive but had very low weight efficiency. The primary driver was manufacturing Mills had limited capacity to roll wider sections. However, as Mill rolling capacities improved, it allowed sheet pile designers to generate wider pile sections. This provided real savings in strength to weight ratios, since steel can be maximised in the flanges (increasing bending strength) and increasing the distance between the webs, which has the effect of reducing the amount of steel devoted to the leg (web) which does not contribute to bending moment capacity.
This principal has influenced piling shape to ever larger and wider sections. The effect is not insignificant, converting from a narrow, inefficient pile to a wide modern pile, can save up to 27% on weight whilst offering equivalent driveability and strength. A fact not missed by designers and Clients, since steel is sold by the tonne.
In the UK the “standard” sheet pile was the 400 – 420mm wide U pile for several decades. It was quite wasteful, i.e. the weight per square metre in comparison with the Elastic Section Modulus achieved was quite high. However, this high cross sectional area allowed them to be driven into very hard conditions. It also allowed, in some circumstances, poor driving practices to be used, relying on the spare driving capacity of the sections.
In the 1980’s, the 525mm wide range overtook the older sections, offering much higher strength per unit weight, but with reduced capability to withstand sub-optimal driving practice. This range established the template of available Section moduli as 600, 900, 1200, 1600, 2000, 2500, to 3200. This template is still the basic comparator on U piles today.
However, at this same time Z piles were introduced in Mainland Europe. There had been a range named Frodingham in the UK previously but the new Z piles were far more efficient due to their increased width. Despite initial reticence from a market used to driving narrower piles in singles, the weight and hence cost savings of these new Z piles could not be ignored. Indeed it was in an attempt to compete with these new Z piles that wider U piles were introduced in the 90’s. The 600mm wide U pile was initially resisted because of fears over driveability, but the efficiency and need to compete with Z piles soon overcame these reservations. The 600mm wide U pile is still the standard temporary works U pile today.
However, the Z pile has a very important benefit over the U pile in that the U Pile wall has its interlocks on the Neutral Axis of the wall. Since this is the zero bending moment position it is also the maximum shear position. Thus the discontinuity is positioned exactly where continuity is required to transmit the shear forces of the wall. Crimping or welding of interlocks can be adopted to prevent the possible interlock slip (Reduced Modulus Action) but this has to be over the full length and compromises which installing plant can be used and can increase cost significantly.
The advantage is even more pronounced when considering the contribution to overall wall strength made by the interlocks. In the U pile the interlocks do not contribute to the bending strength since the distance from the interlock to the neutral axis is zero, this is wasteful of the steel area in the interlocks. The Z pile interlocks on the other hand the make a significant contribution to overall bending strength. In BS EN 1993-5, these effects are recognised. The U piles are downgraded by reduction factors which acknowledge the possibility of Reduced Modulus Action and the far more complex Orthogonal bending effect. In the UK the actual reduction factors are specified in the UK National Annex to Eurocode 3 Part 5. Reductions for U piles can be very high indeed whereas these penalising reduction factors are not applicable to Z piles.
Today we see ever wider piles with U piles up to 750mm wide and Z piles up to 770mm wide. These piles offer maximised economy (optimised strength to weight ratio) but have clever additions such as strengthened shoulders to ensure drivability is not compromised.
Developments in steel strength
As important as the developments of the sheet piles in terms of shape have been, the actual strength of the steel used has changed dramatically.
In the 1960’s steel piles were offered in grade 43A (with a yield of approximately 270 N/mm2). Later a “High Yield” grade was introduced in grade 50B (with a yield of approximately 350 N/mm2). In today’s market S270GP (the successor of 43A) is quite rare and is generally not strong enough for normal requirements. The generally recognised “basis grade” for sheet piles is S355GP (the successor of 50B).
However, stronger grades are now generally available in S390GP, and S430GP, with yields of 390 N/mm2 and 430 N/mm N/mm2 respectively. In the next version of EN 10248 an even higher grade will available in S460GP with 460 N/mm2 yield.
These higher grades bring several benefits. Clearly, if possible, it is economical to design in a higher grade rather than needing a larger pile section (as long as serviceability requirements are still met). Also the installing contractor may have reservations about getting full penetration with a specific pile and grade combination. It is an effective solution to increase the grade to offer better installation capacity again saving the need to use a heavier section. Finally, a higher grade assists with durability. If, over the life of a marine sheet pile wall, corrosion is expected to claim half the pile thickness, use of a higher grade means that the residual strength of the wall is enhanced. This can either facilitate more economic design or longer design life for the structure.
Quite recently the chemical composition of the steel itself has been enhanced to promote the resistance to corrosion in the Marine Environment. At the beginning of the decade ASTM A 690 (American Grade Standard) was offered because of its enhanced ability to resist corrosion in the Splash Zone (but notably not in the intertidal nor permanent immersion zones).
In 2010 a new Alloy Steel was launched called AMLoCor. This chemistry of steel has been configured to allow the designer to use it as a Carbon Steel but it can enhance the design life in marine zones. It has been proven to reduce the corrosion rate in the Permanent Immersion zone by a factor of three and in the Low Water Zone by a factor of 5. This will potentially revolutionise the design of marine walls where paint protection or cathodic protection may no longer be required and indeed the pile section may be reduced to a more economical size as well.
Steel sheet piles most usually specified in the UK are hot-rolled sections, manufactured in accordance with EN 10248. The sections widely available are described in the Arcelor Piling Handbook and other manufacturers’ literature. These sections are available in strength grades ranging from S240GP to S430GP.
Special steel grades like S 460 AP, American ASTM A 572 steel grades, steels with improved corrosion resistance like AMLoCor® and ASTM A 690, or steels with copper addition in accordance with EN 10248 Part 1 Chapter 10.4 can be supplied on request.
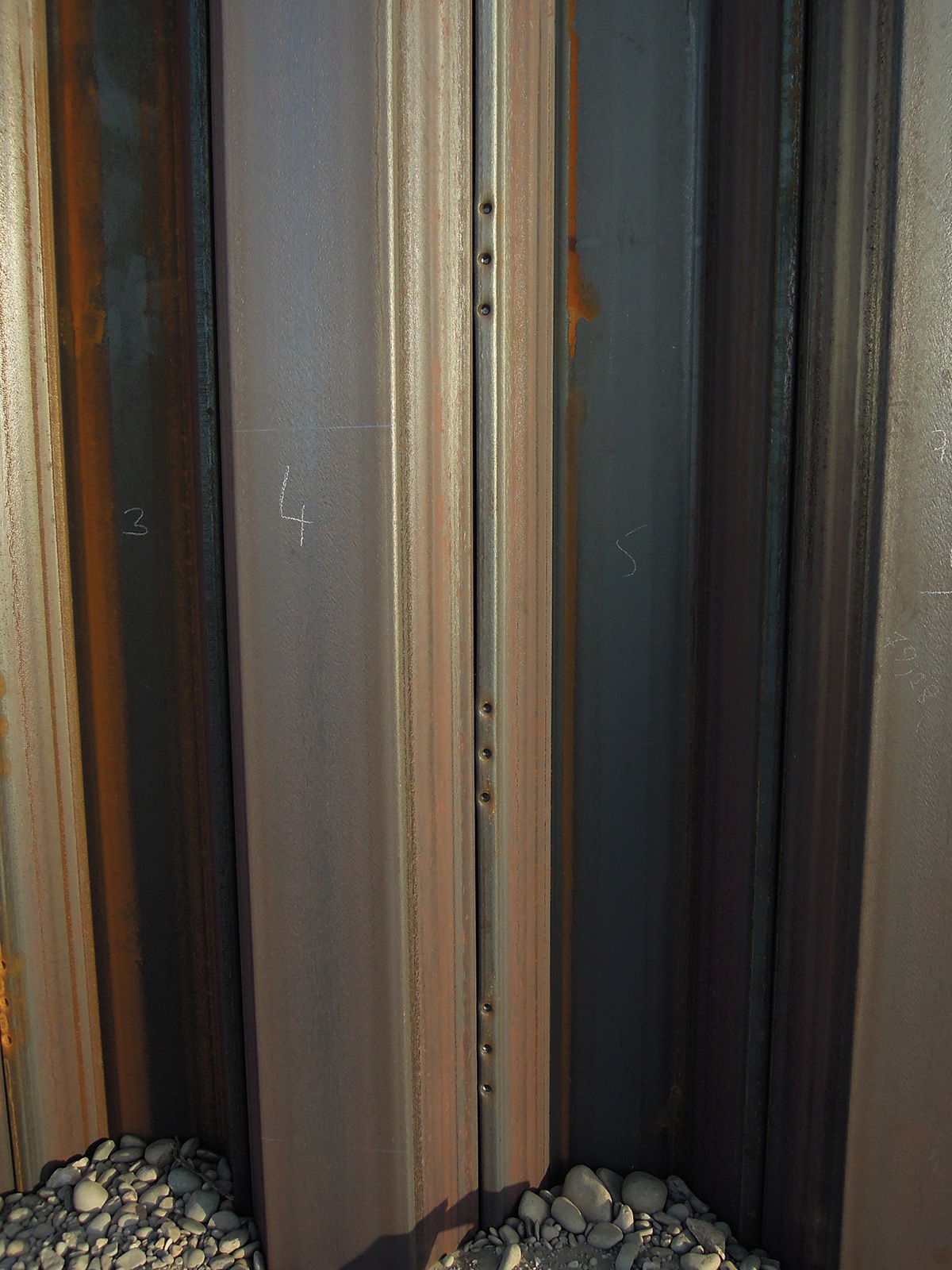
Case Studies
A selection of our work
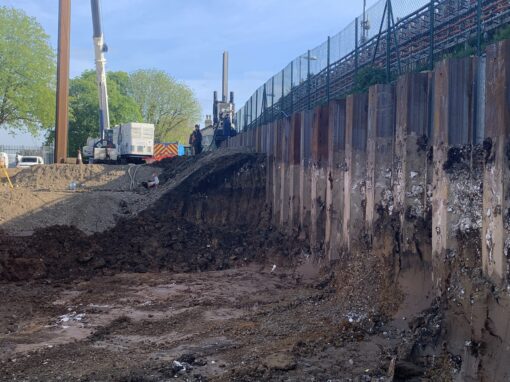
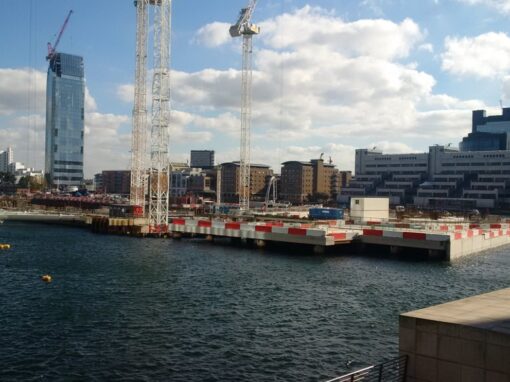
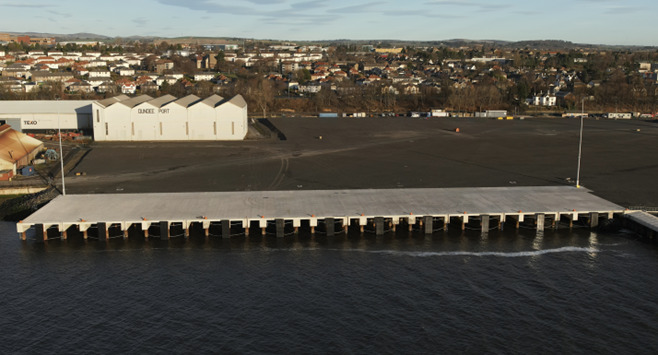
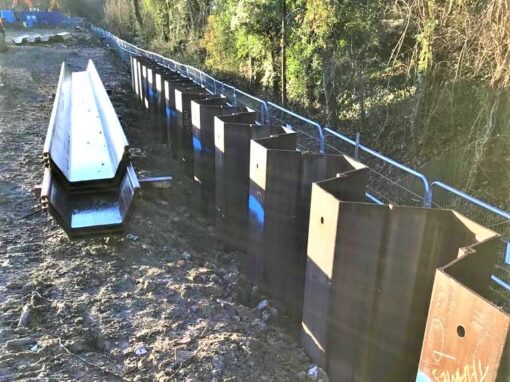

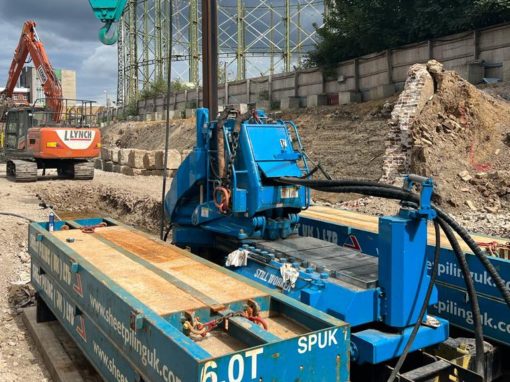

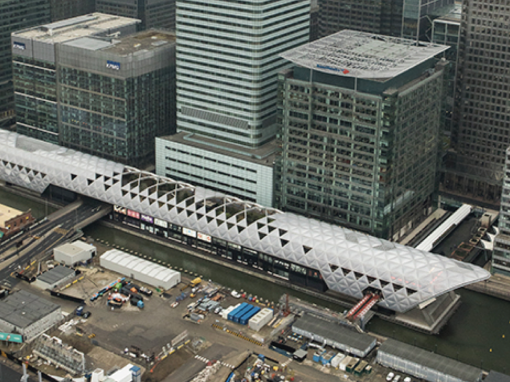
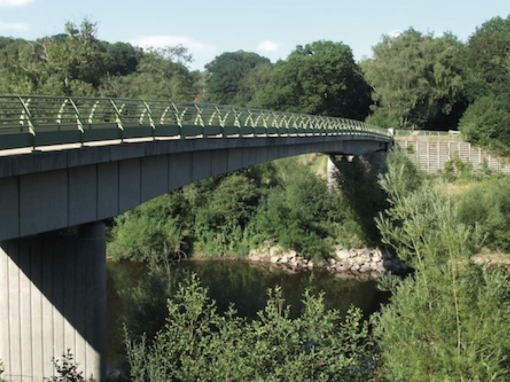
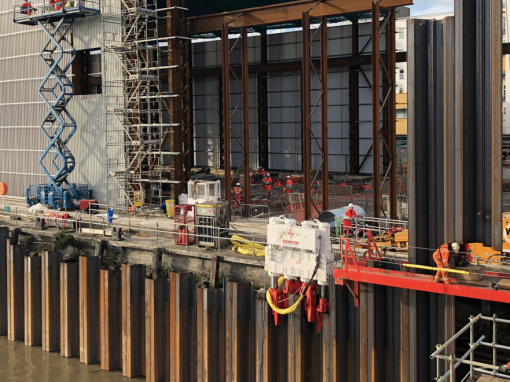
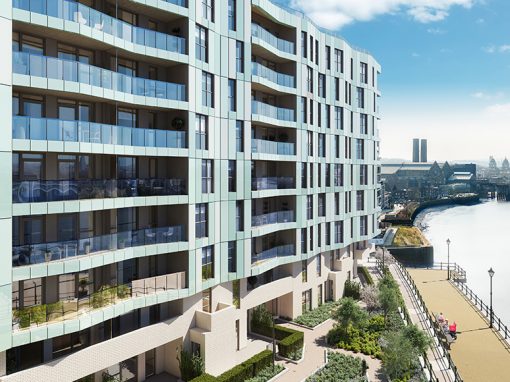
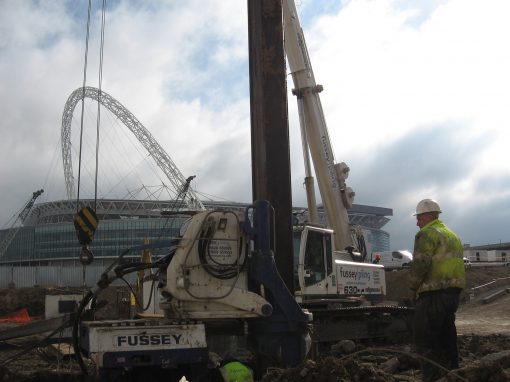
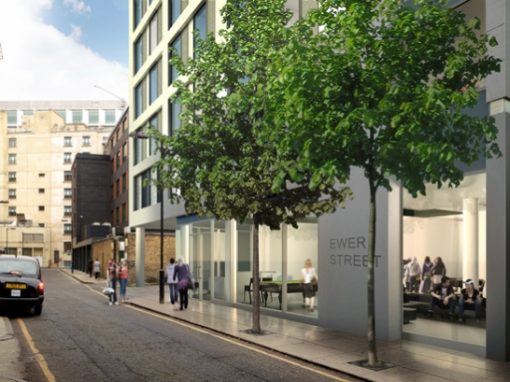
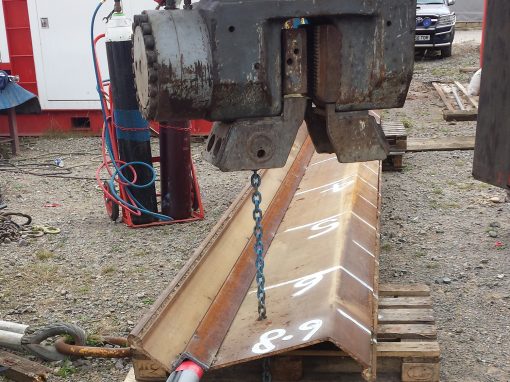
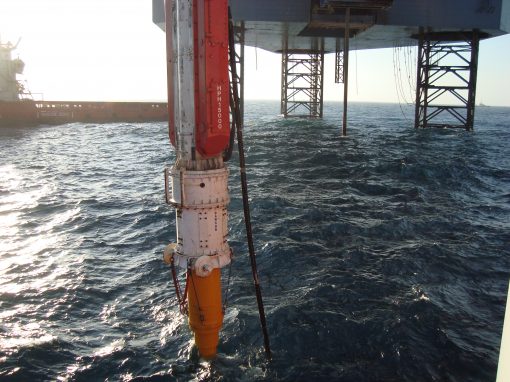
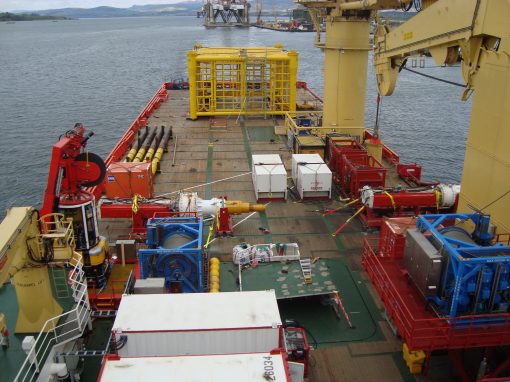
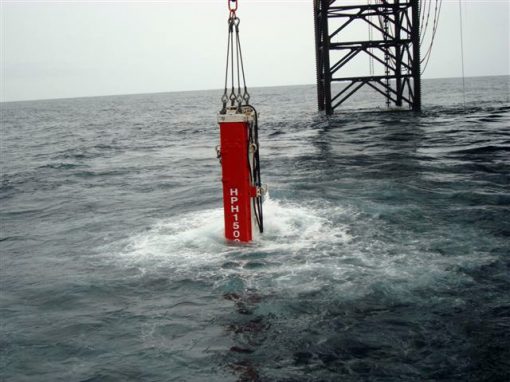
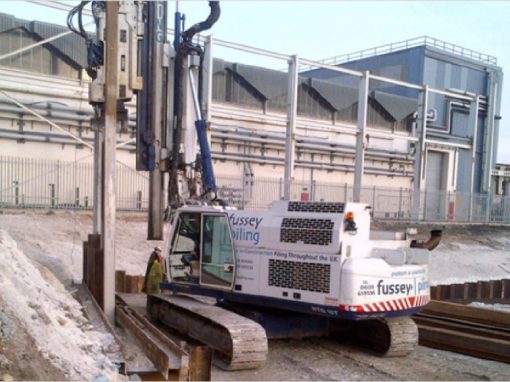
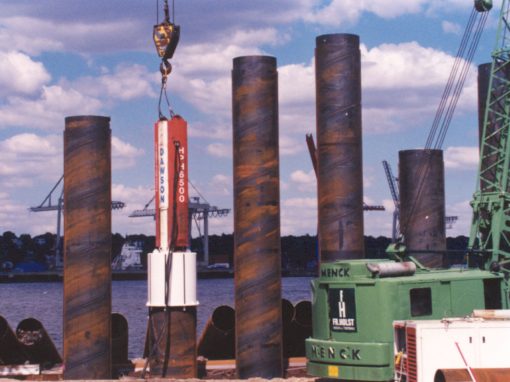
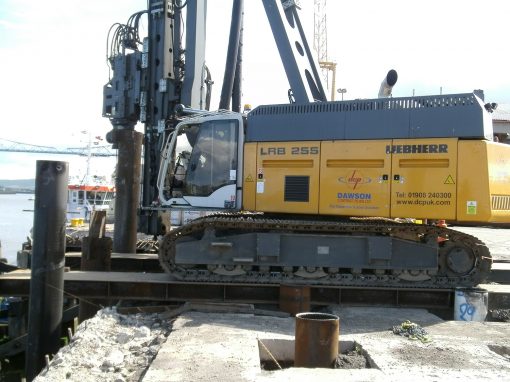
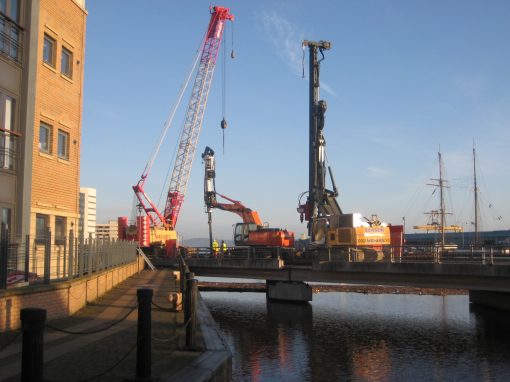
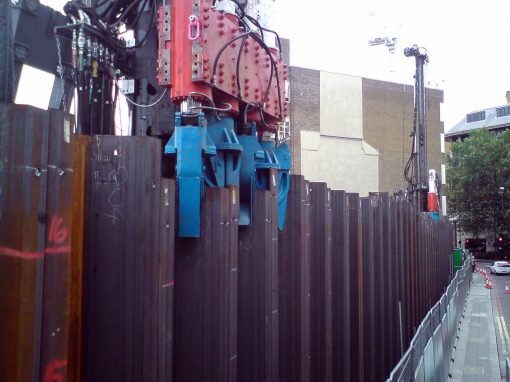
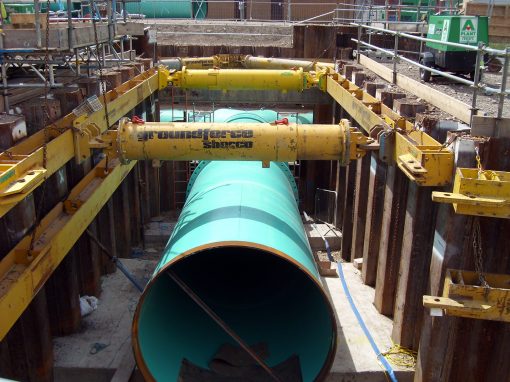
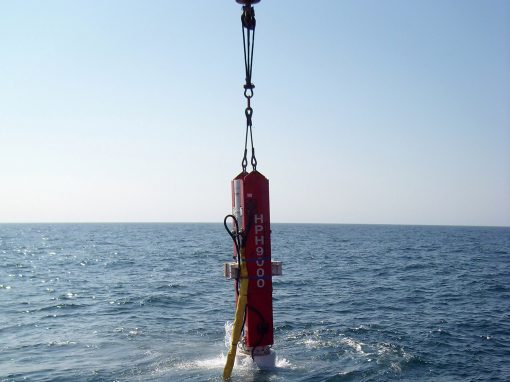
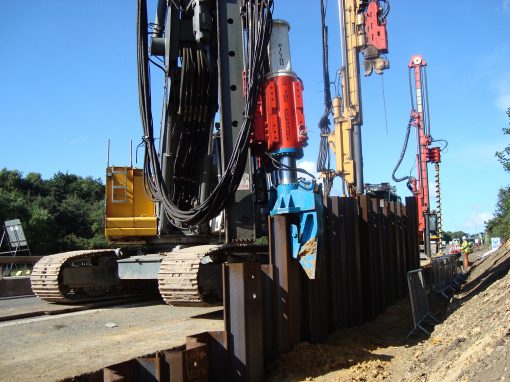
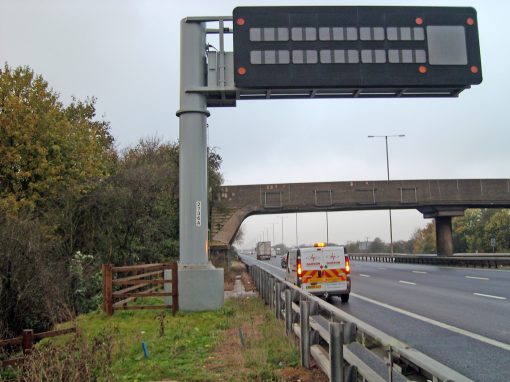
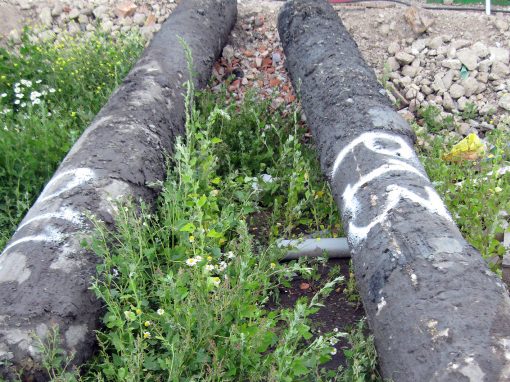
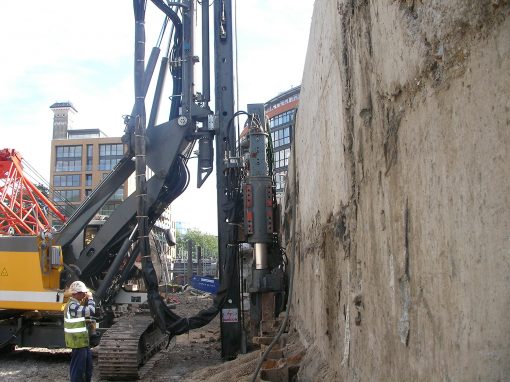
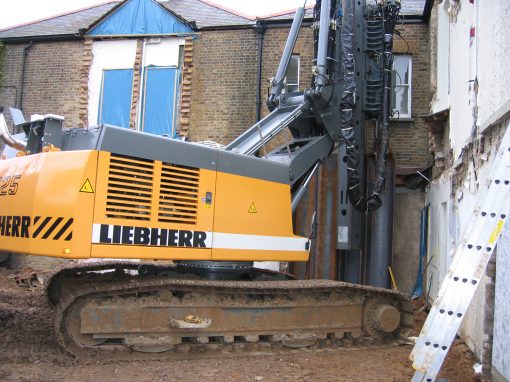
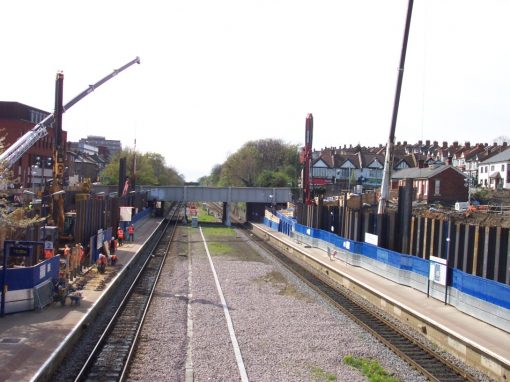
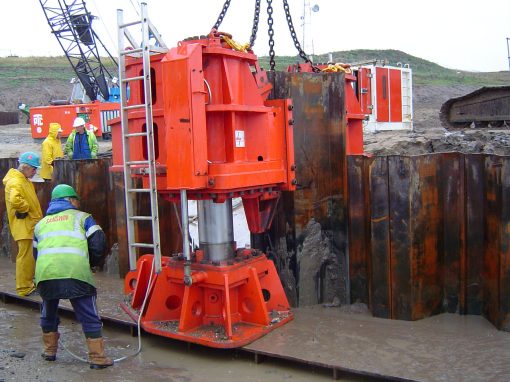
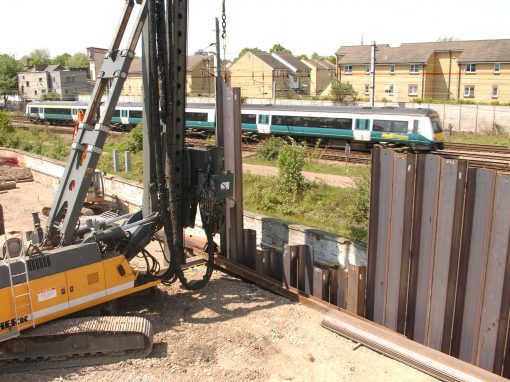
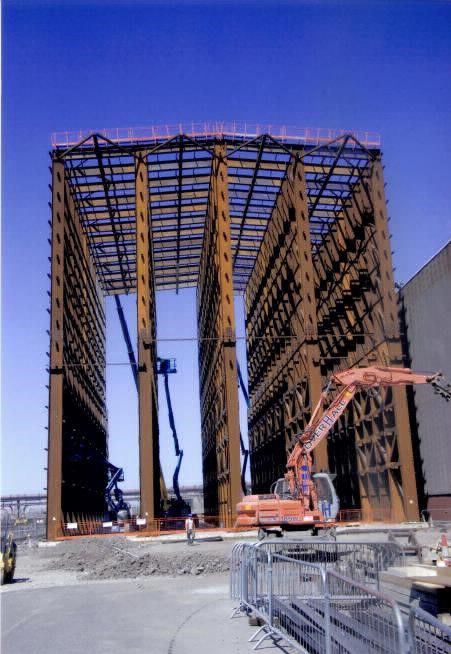
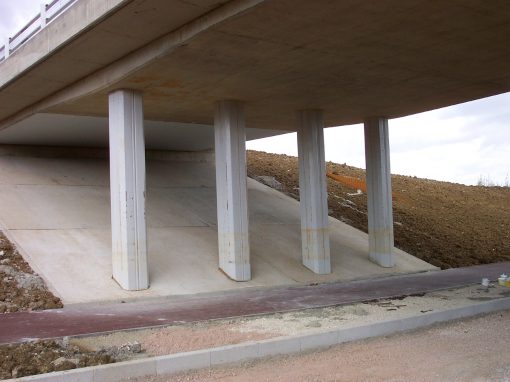
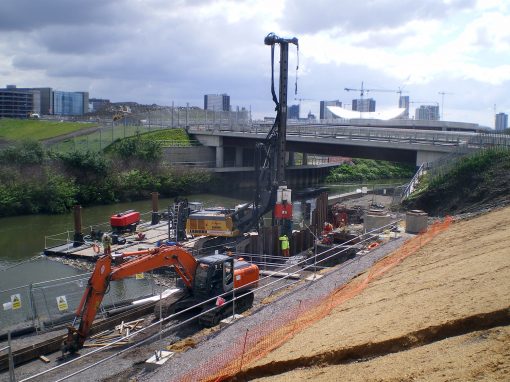

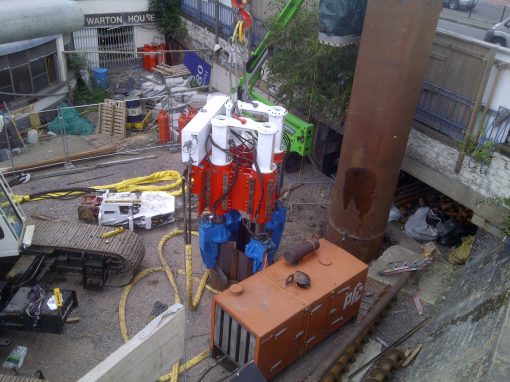
Steel Piling Group, C/O SCI, Silwood Park, Unit D, Buckhurst Road, Ascot ,Berkshire. SL5 7QN
E: info@steelpilinggroup.org
© Copyright 2018 Steel Piling Group
Terms & Conditions | Privacy Policy